Porosity in Welding: Identifying Common Issues and Implementing Ideal Practices for Avoidance
Porosity in welding is a prevalent problem that typically goes unnoticed until it creates considerable issues with the integrity of welds. This common issue can jeopardize the stamina and resilience of welded frameworks, presenting safety threats and causing expensive rework. By comprehending the origin causes of porosity and applying efficient prevention approaches, welders can substantially improve the top quality and dependability of their welds. In this discussion, we will certainly explore the vital variables adding to porosity development, examine its detrimental impacts on weld performance, and go over the best practices that can be adopted to decrease porosity occurrence in welding procedures.
Usual Root Causes Of Porosity
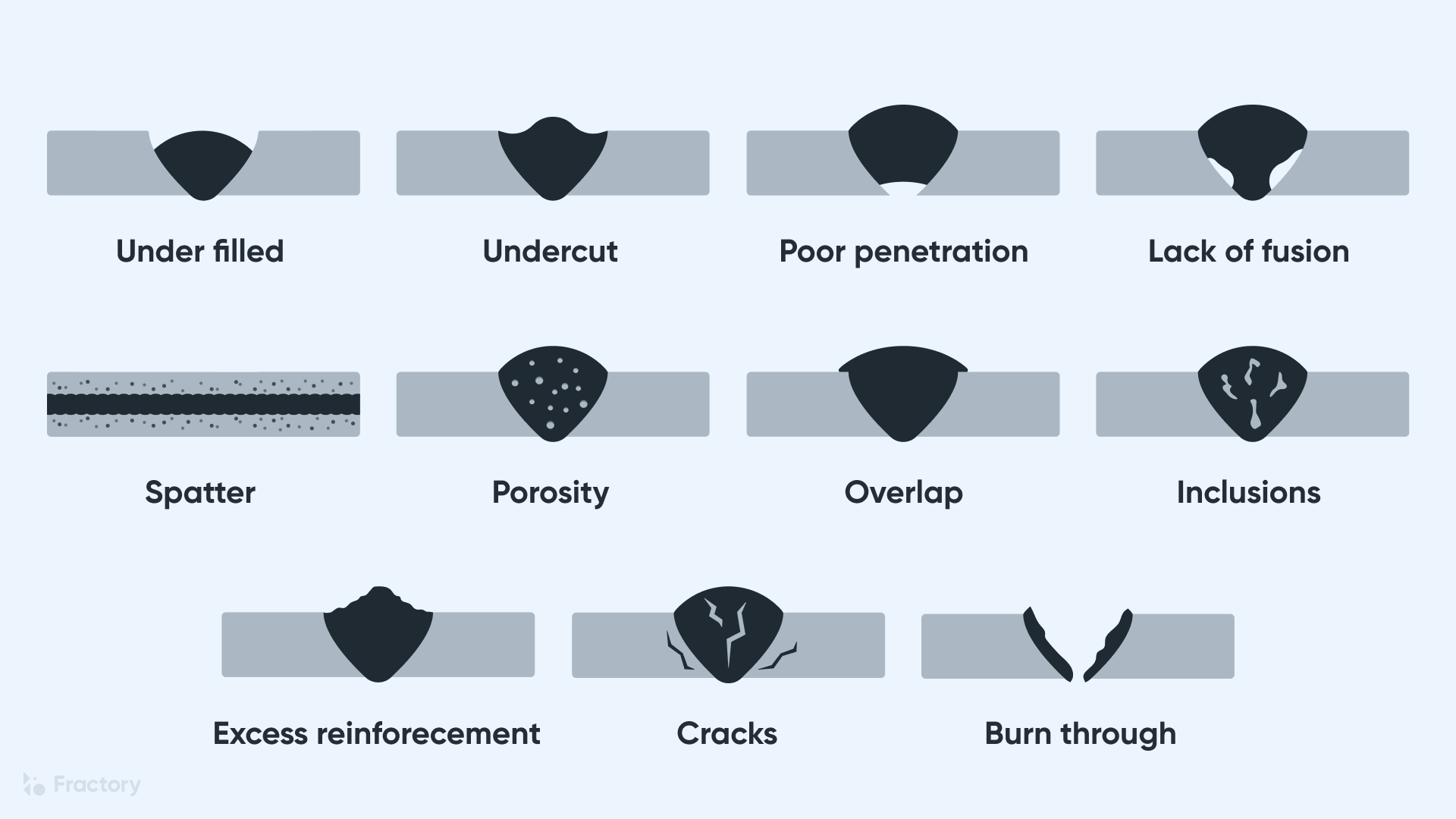
One more regular perpetrator behind porosity is the existence of pollutants externally of the base steel, such as oil, oil, or rust. When these impurities are not efficiently eliminated before welding, they can vaporize and become trapped in the weld, creating issues. Furthermore, making use of unclean or damp filler materials can present contaminations right into the weld, adding to porosity problems. To reduce these typical sources of porosity, detailed cleansing of base metals, proper securing gas option, and adherence to optimum welding specifications are crucial practices in attaining high-grade, porosity-free welds.
Influence of Porosity on Weld High Quality

The presence of porosity in welding can dramatically jeopardize the architectural stability and mechanical residential or commercial properties of bonded joints. Porosity creates gaps within the weld metal, deteriorating its overall toughness and load-bearing capacity. These gaps work as stress and anxiety concentration points, making the weld extra vulnerable to fracturing and failure under applied loads. Furthermore, porosity can lower the weld's resistance to deterioration and other ecological aspects, further reducing its long life and performance.
Among the key effects of porosity is a decrease in the weld's ductility and durability. Welds with high porosity degrees tend to show lower impact toughness and reduced capability to flaw plastically before fracturing. This can be particularly concerning in applications where the welded elements go through vibrant or cyclic loading conditions. Porosity can hamper the weld's capability to properly transmit forces, leading to early weld failing and prospective security risks in vital structures. What is Porosity.
Finest Practices for Porosity Prevention
To boost the structural integrity and quality of welded joints, what particular steps can be implemented to reduce the occurrence of porosity during the welding procedure? Porosity prevention in welding is crucial to make certain the stability and strength of the final weld. One reliable method appertains cleaning of the base steel, eliminating any pollutants such as rust, oil, paint, or dampness that could bring about gas entrapment. Ensuring that the welding tools is in excellent condition, with tidy consumables and proper gas flow prices, can also substantially decrease porosity. In addition, maintaining a stable check that arc and controlling the welding criteria, such as voltage, current, and take a trip speed, helps develop a consistent weld swimming pool that minimizes the danger of gas entrapment. Making use of the appropriate welding strategy for the specific product being welded, such as readjusting the welding angle and gun position, can even more protect against porosity. Normal assessment of welds and prompt remediation of any type of concerns recognized during the welding process are important techniques to stop porosity and generate top quality welds.
Significance of Proper Welding Strategies
Applying correct welding techniques is critical in making sure the structural honesty and high quality of bonded joints, building on the foundation of efficient porosity prevention steps. Welding strategies directly affect the general toughness and longevity of the bonded framework. One essential aspect of correct welding strategies is maintaining the proper warmth input. Too much warmth can result in enhanced porosity as a result of the entrapment of gases in the weld pool. Alternatively, not enough warmth may result in incomplete combination, producing potential weak factors in the joint. Additionally, utilizing the appropriate welding specifications, such as voltage, existing, and take a trip rate, is critical for attaining sound welds with very little porosity.
Additionally, the selection of welding process, whether it be MIG, TIG, or stick welding, need to line up with the particular demands of the job to ensure optimum results. Appropriate cleansing and prep work of the base metal, as well as picking the appropriate filler material, are likewise necessary components of skilled welding methods. By sticking to these finest YOURURL.com methods, welders can lessen the danger of porosity development and create premium, structurally audio welds.

Testing and Quality Assurance Procedures
Checking treatments are necessary to identify and stop porosity in welding, ensuring the toughness and sturdiness of the final product. Non-destructive testing methods such as ultrasonic testing, radiographic testing, and aesthetic examination are frequently utilized to determine potential defects like porosity.
Post-weld inspections, on the other hand, analyze the final weld for any type of defects, including porosity, and verify that it fulfills specified requirements. Applying an extensive top quality control plan that includes detailed testing procedures and inspections is extremely important to reducing porosity problems and guaranteeing the total quality of welded joints.
Verdict
Finally, porosity in welding can be an usual concern that influences the quality of welds. By determining the typical reasons of porosity and executing best practices for avoidance, such as correct welding strategies and testing procedures, welders can make certain top quality and reputable welds. It is necessary to prioritize prevention approaches to minimize next page the event of porosity and maintain the integrity of welded frameworks.
Comments on “Professional Guidance on What is Porosity in Welding and Just How to Address It”